Leak Testing of Electronic Components
Since electronic devices are now present in every aspect of our lives, the sealing of electronic components has become increasingly significant for manufacturers. As we transition from analog technologies to systems with electronic circuit boards, we carry products like phones and smartwatches with us throughout the day, or use products like cars and security cameras in outdoor environments. These products, like us, are exposed to external factors. Pollutants such as dust, sand, and dirt, as well as fluids like rainwater and water vapor, can have a negative impact on the operation of electronic components. Over time, there has been a need to classify the resistance of products to the aforementioned external factors. This classification is referred to as ‘Ingress Protection’ or IP.
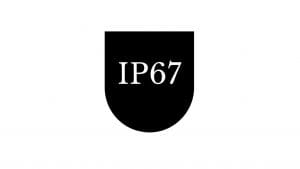
The first digit indicates protection against solid objects. Ranging from 0 to 6, a rating of 6 signifies complete protection against dust, indicating that no dust can penetrate.
The second digit describes the level of protection against liquids and vapors, ranging from 0 to 8. A rating of 1 indicates continuous protection when immersed in water deeper than 1 meter.
Which products should we conduct leak testing on within the scope of IP standards?
We previously discussed how exposure of electronic components to dust, dirt, and vapor can have negative effects on products. These negative effects include corrosion, short circuits, or performance issues. To prevent these outcomes, the parts that require leak testing are as follows:
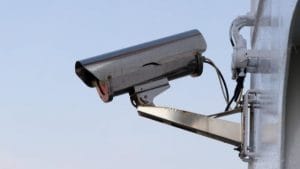
Leak Testing Components in Other Industries
All electronic products expected to be exposed to environmental conditions. You can check here to see the applications and references for the leak testing we perform on electronic products.
How are IP67 and Hermeticity Testing Conducted for the Leak Testing of Electronic Components?
IP67 tests are conducted using the Adlema BT 4000 series leak testing device and the Ep 60 test leak testing kit. The product to be tested is placed inside the Ep 60 leak testing kit and sealed securely. Pressurized air is then introduced into the Ep 60 test kit from a reference volume. After the air introduction process, the stabilization phase begins.
The stabilization phase is necessary to allow the pressurized air inside the test kit to reach a state of equilibrium and exclude pressure drops caused by stagnation and expansion from affecting the test result. If the tested product is leak-free, the pressure remains constant throughout the test duration. Based on pre-defined parameters, the Adlema BT 4000 leak testing device automatically determines whether the product meets the desired standards. Products that receive approval are ready for use.
Electronic Components Undergoing Leak Testing
- Phone,
- Laptop,
- Watch,
- Microphone,
- Camera,
- Sensor,
- Street lamp,
- Security cameras
Leakage of Electronic Components in the Automotive Industry
- Sensors,
- Headlights,
- Electric vehicle batteries,
- Adapters,
- Cables
Contact us for parameters, test set-up or any questions you may have.